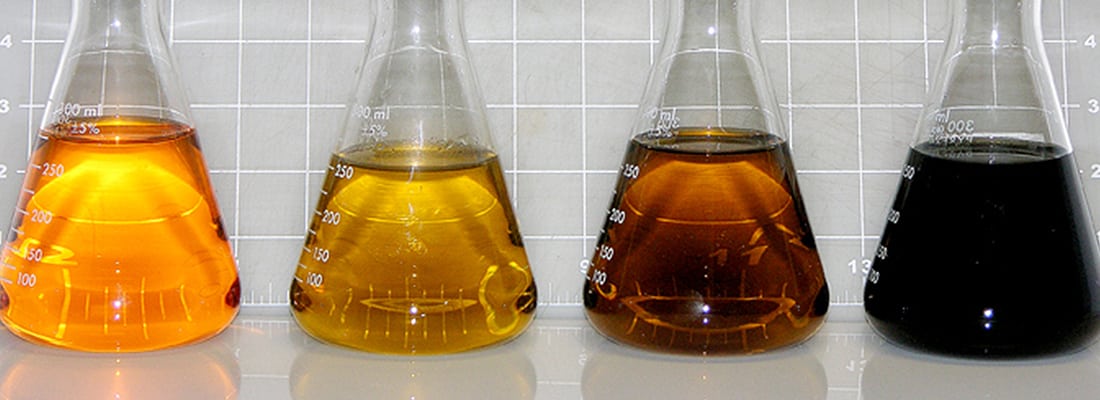
POLARIS Laboratories® has shaken up how we perform particle count testing at our U.S. location, and I’m excited about the improvements we’ve seen so far. In order to continue providing customers with top-notch oil analysis service, we switched from using the ISO 11500 test method to ASTM D7647 utilizing a solvent dilution test method.
There is nothing wrong with the equipment performing the ISO 11500 test methods, but we relied on pore blockage testing – an alternative particle count test – for dark samples or water-soluble fluids.
A few years ago, the manufacturer ceased supporting our pore blockage instruments. The effort to maintain the ageing equipment continued to rise, and POLARIS Laboratories® faced the choice of simply replacing the units or consolidating particle count and pore blockage testing into one instrument. We concluded the latter would be better for our internal processes at the same time it improved the service we provide customers.
By setting aside the good to accomplish the great, we knew we would face difficulties that always accompany change. First of all, it meant only the U.S.-based instruments would be replaced, leaving our labs in Edmonton, Guatemala City, and Poznan running ISO 11500 on the current units. While we now have plenty of spare parts for those units, we need to maintain two different test methods until we’re ready to switch over the rest of the locations.
It took about a year to validate the instrument’s capabilities, demonstrate the new method would match or outperform the current process, and organize the laboratories for the change. All of the preparation allows us to be confident we can switch to ASTM D7647 and provide a higher quality test results without a service interruption.
But changing test methods will benefit customers as well. The ISO 11500 test method results sometimes included water and soft, non-damaging particles (such as varnishes and long-chain additives) along with the hard particles that pose a danger to equipment longevity. The solvents we are using in ASTM D7647 allow the results to better represent the particle count of fluid under those conditions. Customers currently receiving pore blockage testing should see a mild shift in particle count results as a result of the new method.
To learn more about the different particle count test methods, the ISO cleanliness code, and how particle count tests results help you extend equipment life, explore our particle count technical bulletins or contact our data analysis team.
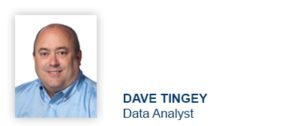
Proven Impact. Proven Uptime. Proven Savings.
Let us prove it to you.
Published March 21, 2017