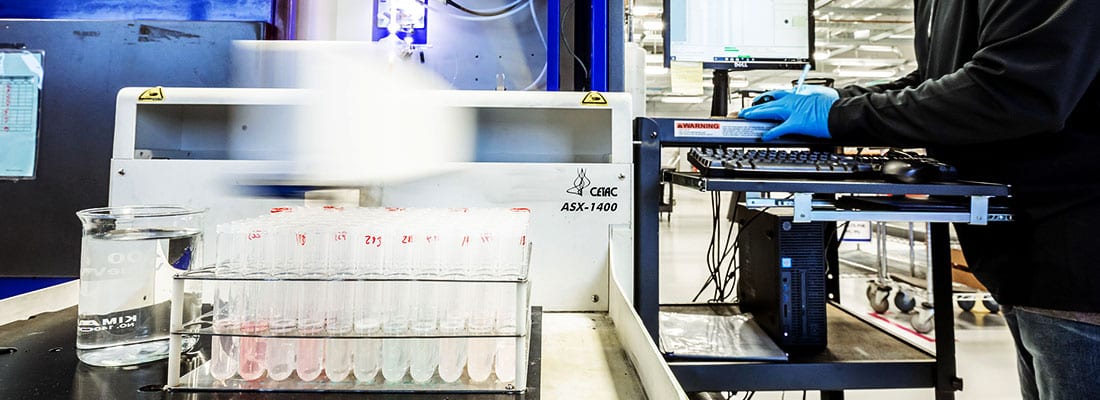
40 to 50 percent of preventable premature engine failures can be traced back to problems in the cooling system
The majority of those failures are due to issues in the cooling system that can be identified early with coolant sampling
The Importance of Adding Coolant Testing into Your Program
Have you lost an engine and wish you could have caught the problem before the point of no return? Or better yet, what if you could determine the root cause all together? Adding coolant testing to your existing program can do exactly that.
Only monitoring the lubricant provides a limited view of a much bigger picture.
Research has found that when physicians take a whole body approach, their patients heal faster, have a higher success rate, and have a more favorable response to a prescribed medication or therapy. In thinking about our equipment, we should take a similar approach. If you are not testing your coolant, you are ignoring half the patient and half the problems.
As engine metallurgy and design have become more advanced and the demand for increased fuel efficiency and emission’s, engine operating temperatures have increased more than 40 degrees Fahrenheit in the last 50 years. This puts a greater emphasis on maintaining the thermal loads placed on the modern cooling systems.
Some common issues that can be detected and addressed with coolant testing include:
1. Identifying incorrect glycol concentration
There are many causes for the glycol concentration to not be at the proper ratio. Some of the common causes include system top offs with water or coolant concentrate, loss of water due to boil off from a defective pressure cap, and/or flush water left in the system. When glycol concentration is not at the proper ratio per OEM specification problems occur including coolant and engine block freezing, seal damage, and/or overheating. This reduces the life of the lubricant and may cause premature engine failure.
2. Are your pH levels out of specification?
Monitoring the coolant pH levels will indicate early concerns within the cooling system. An engine coolant’s acceptable pH level varies depending upon the coolant formulation. Issues that may arise when pH is out of specification include corrosion of iron components and other metals which often results in pitting of engine liners. Also, corrosives will attack the EGR coolers, or any other cooler in the system. The problem is exacerbated when corrosion protection inhibitors drop out of solution which causes plugging and inadequate coolant flow. When coolant cannot properly circulate, heat cannot be removed efficiently from the engine and the lubricant degrades more quickly resulting in shorter drain intervals.
3. Inadequate corrosion protection inhibitors
The purpose of corrosion protection inhibitors are to maintain pH, prevent foaming and prevent internal metal surfaces from corroding. When corrosion exists in the cooling system heat will not be efficiently removed. Additionally, a corrosive environment will attack most solder joints causing holes and leaks in the system. These leaks will in themselves cause secondary issues including internal coolant boiling, contamination, and adverse chemical reactions.
4. Find sources of contamination
There are many possible sources of contamination which cause damage to the cooling system and ultimately the engine. For our purposes, we will focus on the most preventable source: water, which is used to dilute coolant concentrate or top-off the system. Using water that does not meet ASTM and/or OEM manufacturer’s specifications will increase scale formation and corrosion potential within the cooling system. Even ‘clean’ tap water may contain magnesium, calcium, sulfate or chloride in levels that are harmful for the equipment. Scale forms where the greatest amount of heat transfer is needed and acts as an insulator resulting in overheating and engine damage.
If you want to learn more about adding water to your cooling system, check out our video here.
5. Detect early failure
Coolant testing can indicate combustion gas leaks, air leaks, glycol degradation, electrical issues and contaminants. Each issue will cause chemical reactions within the cooling system, resulting in failure. With early detection, scheduled down time for repairs can be made. Correcting the issue will help prevent complete engine failure or unexpected downtime.
Corrosion occurs at a slower rate than engine wear. This is why engine failures occur more frequently but are often traced back to issues within the cooling system. The cooling system must be able to circulate coolant, remove heat from the system and dissipate the heat in order to function correctly. When the cooling system is not able to circulate or remove the heat effectively, we will see reduced life of the lubricant, increased engine wear, and/or issues with system components, which often result in premature engine failure.
Coolant Test Descriptions
See all possible coolant testing, how the testing is performed and what it can tell you about your system:
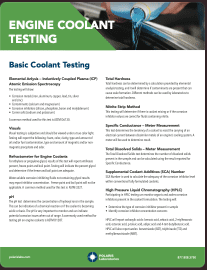
Basic and Advanced Testing
Test all fluids in your equipment!
Testing all fluids within the equipment by utilizing an effective fluid analysis program will help reduce unexpected down times and/or equipment replacements – resulting in an increase return of investment (ROI).
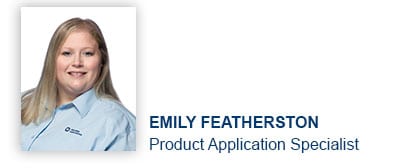
Proven Impact. Proven Uptime. Proven Savings.
Let us prove it to you.
Published April 16, 2019