Cuando miro atrás, me cuesta creer que llevo más de 35 años en el sector del análisis de aceites. Conocí esta ciencia en 1983, cuando estaba en el ejército. Me destinaron a mi primer destino permanente como mecánico de vehículos de vía (MOS 63Y10). A mi oficial de motor le convenció el valor que ofrecía el análisis de aceite y, con el tiempo, yo también empecé a aprender y a creer en ese valor.
¿Qué ha cambiado a lo largo de los años? En primer lugar, el "análisis de aceite" se denomina ahora más comúnmente "análisis de fluidos", ya que en los programas para clientes se suelen analizar otros fluidos, no sólo el aceite.
Entonces: Reactive
En los años 80 y 90, utilizábamos el análisis del aceite para evitar fallos catastróficos. Se podría decir que era un enfoque de mantenimiento "justo a tiempo". Si se recibía un informe de análisis de aceite de alta gravedad sobre una pieza específica del equipo, el equipo asociado con el informe de alta gravedad pasaba a la lista de prioridades de mantenimiento, en la mayoría de los casos un evento de mantenimiento "reactivo".
Ahora: Predicción
Hoy en día, utilizar no sólo el análisis del aceite, sino también el análisis del combustible y del refrigerante, para evitar que se produzcan fallos catastróficos sigue siendo un objetivo primordial. Sin embargo, si termina ahí su enfoque, se está perdiendo y no está aprovechando al máximo lo que estos servicios pueden ofrecer hoy a su programa de mantenimiento.
Las organizaciones de mantenimiento de categoría mundial aprovechan ahora todas las posibilidades que ofrece un programa eficaz de análisis de fluidos. Ya no solo se concentran en prevenir fallos catastróficos, sino también:
- Control del estado del aceiteque permite optimizar los intervalos de drenaje.
- Control de la limpieza de los fluidos: tomar medidas para filtrar y limpiar los fluidos y, al hacerlo, aumentar considerablemente las horas de vida útil de los componentes.
- Control de los aditivos: permite detectar rápidamente si se ha producido una mezcla de lubricantes o una contaminación cruzada
- Pasar del mantenimiento preventivo al mantenimiento predictivo: Con el análisis de fluidos y otras tecnologías de pruebas no invasivas, podemos controlar la salud de los componentes. De este modo, es posible abandonar las viejas prácticas de sustituir o reconstruir los componentes con un intervalo prescrito y realizar reconstrucciones y sustituciones sólo cuando se avisa de que hay que hacerlo.
- Análisis del refrigerante: Para los componentes refrigerados por líquido, el análisis del refrigerante es esencial. Sabía que más del 50% de las averías "evitables y prematuras" de los motores están relacionadas con problemas del sistema de refrigeración?
- Análisis del combustible: En los motores diesel actuales, las tolerancias son más estrictas que nunca. Los problemas con el combustible provocan el desgaste del sistema de combustible, la disminución del rendimiento e incluso averías.
Ya no es reactivo
Un programa de análisis de fluidos de calidad ofrece mucho más. Dado que las capacidades actuales de análisis de fluidos nos alertan de las fases más tempranas del desgaste, podemos planificar y programar las actividades de mantenimiento y alejarnos de los eventos reactivos y no planificados. Al hacerlo, descubrimos que aumenta la disponibilidad de los equipos, mejora la tasa de finalización de las actividades programadas, disminuye en gran medida el riesgo para la seguridad asociado al mantenimiento reactivo, mejora la disponibilidad de los equipos y se reducen los costes de mantenimiento.
Los procedimientos de examen también han cambiado
¿Y los propios procedimientos de ensayo? ¿Han mejorado con los años? La respuesta es sí. Cuando comencé mi carrera, la pizarra de pruebas estándar incluía el control de 18 elementos para las pruebas rutinarias. En la actualidad, la pizarra de pruebas rutinarias estándar de POLARIS Laboratories® incluye 24 elementos, lo que permite controlar el desgaste de los equipos de última generación. Las mejoras no se han quedado ahí. Las mejoras en el recuento de partículas, la dilución del combustible, el hollín, el agua e incluso el software de informes también han experimentado grandes mejoras.
Informe innovador y avances de software
Cuando se trata del software de informes, ya no estamos limitados a revisar un solo informe, sino que podemos identificar rápidamente las causas comunes de los informes de alta gravedad, entre los tipos de componentes comunes y ajustar nuestras actividades y estrategias de mantenimiento para superar los posibles problemas. Las pruebas actuales pueden proporcionar realmente un importante retorno de la inversión y ayudar a que su equipo funcione mejor que nunca.
Para terminar, les dejo este consejo. Identifique los objetivos de su programa de análisis de fluidos y, a continuación, compruebe el perfil de su paquete de pruebas de análisis de fluidos y asegúrese de que la prueba que está realizando su proveedor de servicios incluye la prueba individual para cumplir esos objetivos. Los tiempos y las pruebas han cambiado y no todos los paquetes de pruebas son iguales. Los objetivos y las pruebas deben estar alineados. Si tiene alguna pregunta o desea evaluar su programa actual, le animo a que se ponga en contacto con su laboratorio.
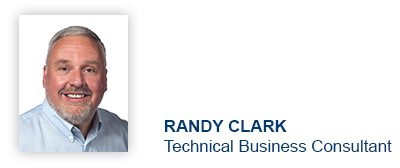
Impacto probado. Tiempo de actividad probado. Ahorro probado.
Déjenos demostrárselo.
Publicado el 24 de julio de 2018