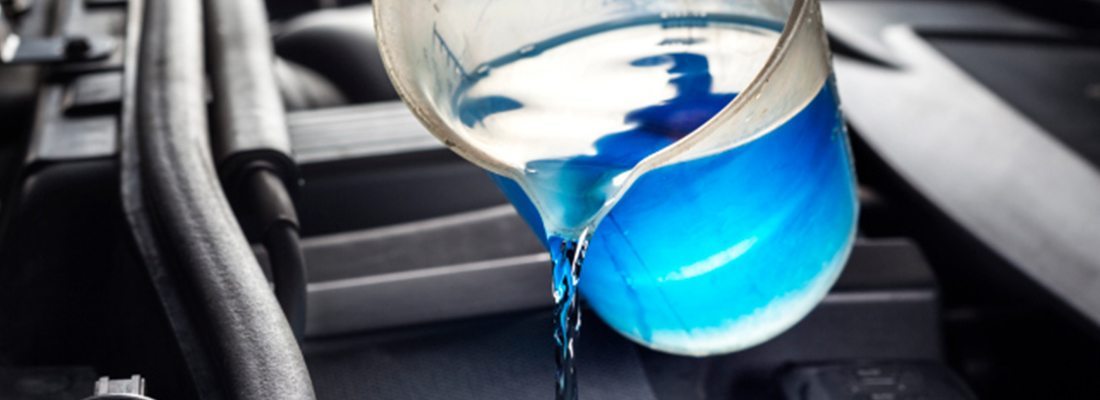
Do you have problems with your equipment’s coolant? While addressing coolant issues may seem as easy as changing your coolant, it’s actually a bit more complicated than that.
Even if you change your coolant frequently, issues with your equipment can and will persist without any visible indicators. If your equipment has inconsistent levels of fluid properties, you’re not addressing the root cause of the issue by changing the fluid. Only routine fluid analysis can direct you to the real cause of the problem.
When it comes to improving your equipment health, it’s essential you have all the information. Not convinced? The following consequences may be enough to change your mind.
Antifreeze/Glycol %:
Too high or low of a percent can cause issues, including: boiling coolant or the block may freeze, cavitation and corrosion, loss of heat transfer, pitted liners, and seals may fail.
pH:
If your coolant becomes acidic, it could cause corrosion on iron components, electrolysis pitting through liners, corrosive attack on engine block and possible corrosion protection chemicals precipitate out of solution.
Specific Conductance:
When this level is in excess, your coolant may lose the ability to resist carrying an electrical current between the dissimilar metals of an engine’s cooling system.
Total Metals:
Abnormal levels of metals is a sign of metal corrosion, liner pitting, and corrosion or erosion of any metal components.
By using fluid analysis to find the root cause of the problem, you can directly address your equipment issues. Learn more about how diagnosing coolant issues through fluid testing can help you protect your equipment by downloading this technical bulletin.
If you’re interested in adding coolant testing to your fluid analysis program, contact your account manager or speak with our customer service team.
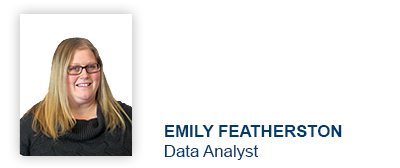
Proven Impact. Proven Uptime. Proven Savings.
Let us prove it to you.