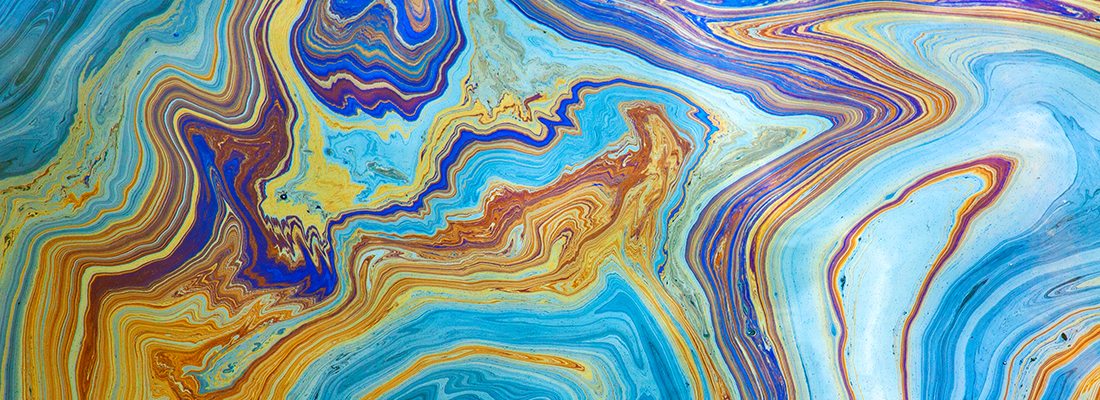
Tailor made to address your biggest challenges
If you’ve ever had anything custom made, you know the feeling. It fits like a glove and meets your needs. It helps you get the job done—and done right. The fact is, there’s inherent value in having something made especially for you or with you in mind.
Imparting this kind of tailor-made value is our goal with the 2015 POLARIS Laboratories® Customer Summit. Sporting the theme, “Driving Action,” this summit will use both our day-to-day experience working with our customers and feedback from our customers to address the topics and challenges YOU—our customer—say are most important. Whether you’re a reseller, distributor, OEM or end user, you’ll find the information, insights and ready-to-implement strategies you need to extend equipment life, increase uptime and realize cost savings.
More detailed programming information about this exclusive, customers-only summit (October 5-7 at the Conrad Hotel in Indianapolis) is available online. For now, I’d like to share with you some of the key takeaways you can expect in October.
First, we’ve structured some of the topical sessions along three tracks—Program Management, Contamination Control and Program Execution. Within the three tracks, we’ll target common concerns, problem areas and frequently asked questions. While you’ll hear from members of our POLARIS Laboratories® team, you’ll also learn from customers just like you who are achieving success with their oil analysis programs. Customers sharing their insights, strategies and successes are what will really set this meeting apart from other conferences you might attend this year.
Here are just some of the program highlights you can expect in October:
Structuring your oil analysis program to fit your needs – Learn how to customize and follow a systematic oil analysis program that considers your organization’s strengths and weaknesses and helps meet your objectives.
Increase equipment uptime – Know and understand which oil analysis recommendations are “musts” and which ones you can schedule for a later time. Finding the right balance about when to take action will help maximize equipment uptime.
Calculate and assess your return on investment – Gain insight into how you can calculate a reliable ROI for your oil analysis program. We’ll show you how in this highly anticipated, must-attend presentation.
Move from preventive and reactive to predictive and proactive – If the 2015 Customer Summit has an overall theme, this might be it. Nearly every successful oil analysis program is more predictive and proactive than anything else. You’ll learn strategies for moving your program beyond short-term, reactive fixes to actions that are forward thinking, reducing the likelihood of equipment damage and increasing profitability.
Take a proactive step now. Register for the summit today – or at least by May 15 – and save $200.
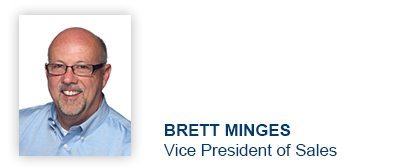
Proven Impact. Proven Uptime. Proven Savings.
Let us prove it to you.
Published March 10, 2015