W Edwards Deming once said, “Learning is not compulsory; it’s voluntary. Improvement is not compulsory; it’s voluntary. But to survive, we must learn.”
And, POLARIS Laboratories® is ready to help you learn…about the future.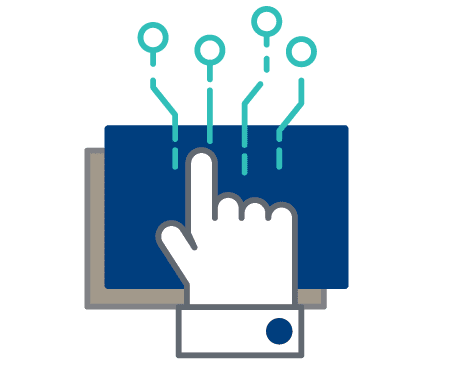
We partner with program champions from companies all around the globe and, together, we have helped them save more of their equipment. Yet, the world is advancing rapidly so we’re committed to helping our customers leverage new innovation, creativity and strategy to improve their programs. By embracing change through proven telematics and connectivity capabilities, maintenance professionals have embarked on a continuous journey to Unlock Reliability.
Now, just imagine how effective your fluid analysis program could be if you could successfully automate the information you receive and then transform those untapped recommendations into business intelligence. Come, let us show you. This will be on full display for three days at our fifth annual Customer Summit in Indianapolis from November 18-20, 2019.
Whether you’re looking to huddle with companies that have proven successes, dive deeper into your program’s performance or learn best practices to design a strategy that transforms information into intelligence, our fifth-annual Customer Summit will provide the keys you need to drive operational performance. With three days of reliability insights, 16 learning sessions, three training workshops, one free program review for current customers and countless hours of peer-to-peer networking, this program is designed not only for you … but a few of your colleagues, too.
Here are a few key day-by-day highlights from this year’s conference:
- Day 1:
- Exclusive behind-the-scenes laboratory tour at POLARIS Laboratories’ headquarters
- Interactive networking reception to help you connect the importance of identifying a reliable root cause to common equipment failures
- Day 2:
- Compelling look into why the future is now when it comes to reliability
- Recognition of our annual Program Champion Award finalists
- Relaxing dinner and reception at an upscale, car storage facility where you can slide behind the wheel and marvel at the engines of these classic, exotic, luxury cars
- Day 3:
- Insights on how to turn early savings into lasting success as you expand your program to involve new locations and testing capabilities
- POLARIS Laboratories’ commitment to the next generation of fluid analysis through connectivity
Join us and learn why reliability matters! The road to fluid analysis success starts right here at the 2019 Customer Summit!
Learn more about the robust agenda and topics, exclusive laboratory tour, hotel accommodations, fees and more. Seating is limited – and hotel rooms are equally limited – at The Alexander Hotel! Clear your calendar November 18-20 and join us in Indianapolis at the 2019 POLARIS Laboratories® Customer Summit, Unlock Reliability.
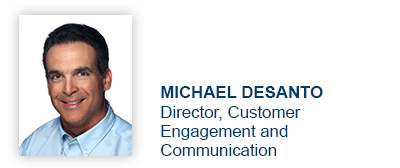
Proven Impact. Proven Uptime. Proven Savings.
Let us prove it to you.
Published August 27, 2019