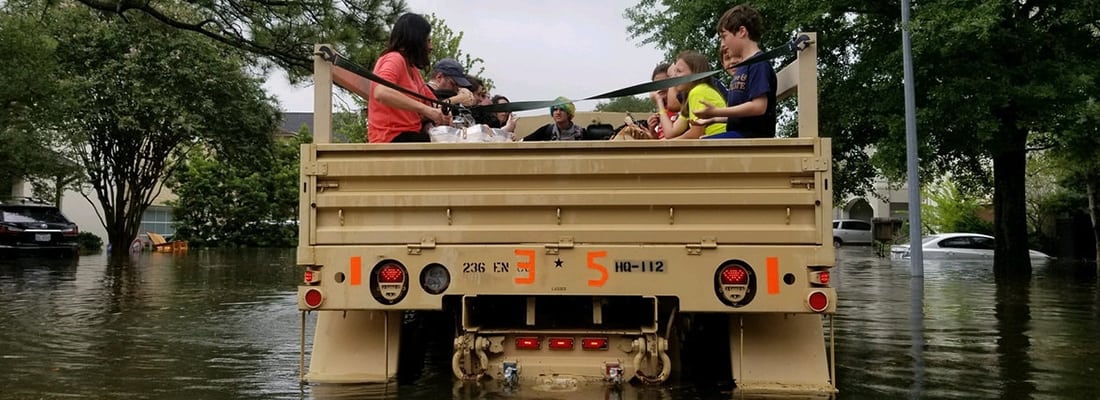
Sometimes it’s hard to plan for destructive natural disasters – such as Hurricane Harvey along the Texas and Louisiana Gulf Coast and the subsequent flooding. So, what do you do if your equipment is exposed to the disaster’s effects and flooding?
Based on years of experience in helping companies save their equipment and extend the equipment’s lifecycle, quite simply we recommend taking action.
Flooding can result in water contamination and can cause corrosion and oxidation which can be extremely harmful for your equipment and, in turn, can cause holds in production and loss of business. How will you know if you need to test your equipment’s fluids to see if any damage was caused and determine if potential maintenance is needed?
First, check for signs of water ingression or leaking. Search for answers to key common challenges, such as:
- Is the high-water mark above the containers?
- Is dried mud crusted on the container?
- Are caps, lids and vents still in place?
- Are desiccant filters saturated?
After you check for signs of water ingression, the next steps for testing depend on the type of fluid:
Oils and Lubricants
Check the fluid itself for signs of water contamination. A milky appearance indicates the oil additives have emulsified as much water as they could, and there is likely more dissolved in the fluid. An oil analysis test from POLARIS Laboratories® includes a water test, and elemental analysis can identify dirt contamination from mud or salt from sea water.
Coolants
Pressure caps on coolant containers typically prevent floodwaters from entering cooling systems. However, it is still worth the time to perform a field test using a refractometer or paper test strip to determine if the glycol/water ratio is still in balance. If you suspect contamination, a coolant analysis test from POLARIS Laboratories® will determine if the external water and dirt requires the cooling system to be drained and/or flushed.
Bulk Tanks
Bulk tanks typically have water drain-off ports to remove free water that settles to the bottom of the tank, but the fluids should be checked for water as well as using the techniques above. A “thief bomb” or “bacon bomb” may be needed to collect the sample. Diesel fuel and new lubricant testing from POLARIS Laboratories® will determine if the fluid quality is adequate for future use.
It’s crucial for any contaminated oils, coolants or diesel fuel to go through analysis testing when flooding occurs. Testing can prevent future issues from arising and can help determine what equipment maintenance is needed to resume work.
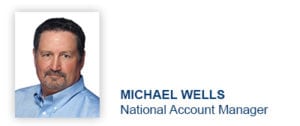
Proven Impact. Proven Uptime. Proven Savings.
Let us prove it to you.
Published September 6, 2017